Our Research
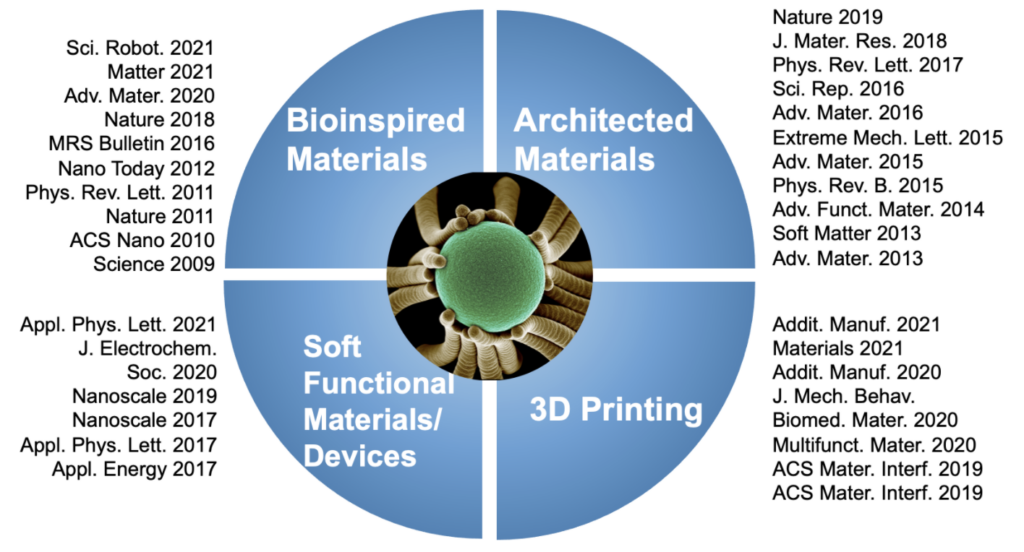
The overarching goal of our research is investigation of the interplay between materials and structures to elucidate the mechanisms for architected/multifunctional materials and devices with extreme functions that can be tailored for their mechanical environments or adapt to the change of the environment with applications for resilience, healthcare, sensing, and energy. To achieve the goal, we find inspiration from nature, study polymer-based materials as constituents of the material system/devices due to their ease of controlling properties and shapes, use finite element methods for designing architectures (structures), investigate 3D printing as tools for fabricating designed structures (architectures) to enable novel mechanical behaviors, and develop experimental tools for validations. Built upon the outcomes of the frameworks, we have been translating the findings and tools to develop resilient and/or self-sustainable materials/structures and novel biomedical devices.
Bioinspired materials and mechanical systems
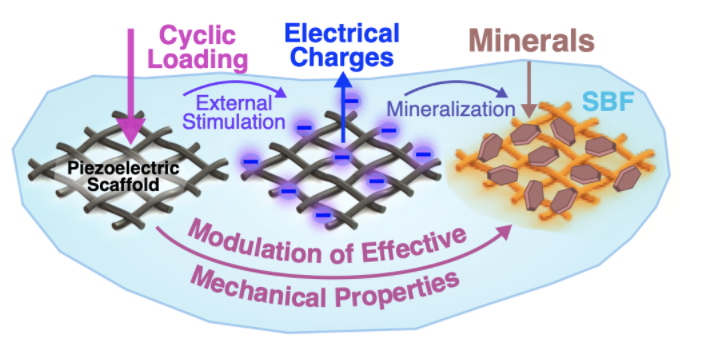
Bioinspired materials with self-adaptable mechanical properties and damage mitigation
Rose prickle inspired devices for sutureless anastomosis
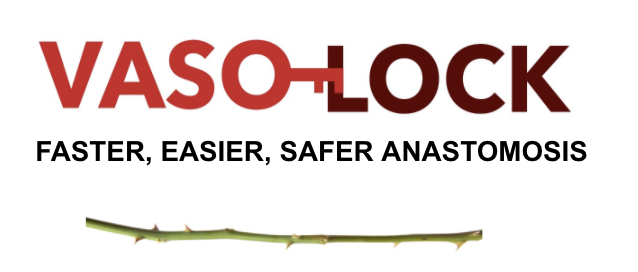
Architected materials
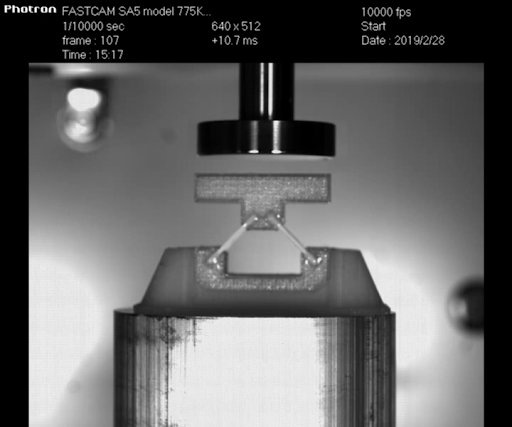
Architected liquid crystalline elastomers for light weight extreme energy absorption
Most materials used to absorb energy from mechanical loading (e.g. helmets, protective gear) undergo plastic deformation and fracture when loaded. This results in irreversible changes in microstructure or material that degrade the performance of the material. Using the interplay between nonlinear materials and nonlinear geometry in architected materials based on liquid crystalline elastomers (LCEs), we have introduced a new mechanism of reversible energy absorption by utilizing snapping instability of elastic materials, which we utilize mechanical deformation of structures to store energy and to release it for repeated uses. This project was done in collaboration with the ARO.
Self-adaptable cardiovascular implant devices to accommodate the growth of pediatric patients
Over 40,000 infants per year are born with congenital heart defects that limit the blood flow from the heart to the lungs. This is usually treated with the implantation of a tube between the right ventricle of the heart and the pulmonary artery, but due to the fast growth rate of children, the child must undergo many surgeries in order to swap out the tube for a larger one as they grow. To address this issue, we utilized folded structures (inspired by organisms such as sea anemones) for diameter changes to enable cardiovascular implants that can “grow” as a response to physiological changes such as blood flow rate increase, allowing the implant to grow over time alongside the child. This project was done with the NIH R21.

3D Printing
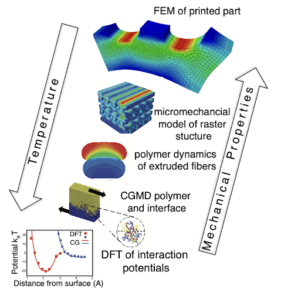
Mechanical properties of polymers 3D printed using fused filament fabrication
Fused filament fabrication (FFF) based on extrusion of molten thermoplastic materials is the most widely used 3D printing technology due to the low cost and printer simplicity. However, applications of FFF printed materials are limited due to inferior mechanical properties and large variability in material properties and dimensions. We studied this issue by looking at the effects of 3D printing parameters including layer height, printing speed, print head temperature, and environment temperature/humidity on the 3D geometry of printed parts using micro CT for quantitative understanding. This project was done with support from the NSF DMREF.
3D printing of soft, durable, biocompatible elastomer
Soft elastomers are particularly important for biomedical applications because they can provide similar mechanical properties as tissues with improved biocompatibility. However, there are very few biocompatible elastomers with 3D printability, and little is known about the material properties of biocompatible 3D printable elastomers. We investigated a new framework to 3D print a soft, biocompatible, and biostable polycarbonate-based urethane silicone (PCU-Sil) with minimal defects. This project was done with support from the NIH R21.
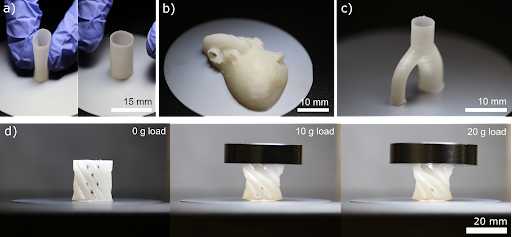
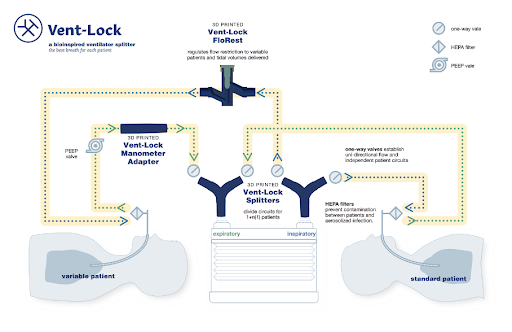
3D-printed ventilator multiplexer to enhance the capacity of treating patients with COVID-19
Soft functional materials and devices
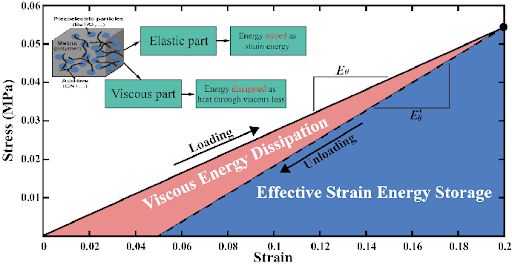
Flexible and tunable energy harvesters
Soft composite-based pressure sensor
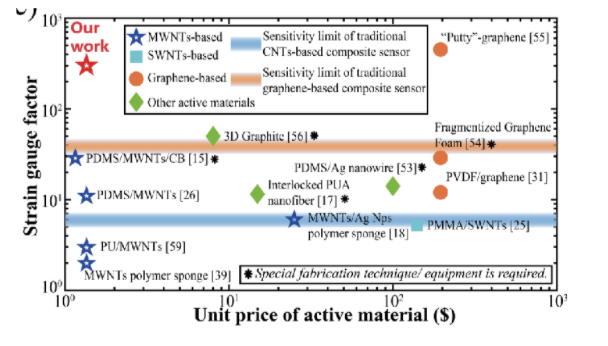