Publications
Li, Jing; Orrego, Santiago; Pan, Junjie; He, Peisheng; Kang, Sung Hoon
Ultrasensitive, flexible, and low-cost nanoporous piezoresistive composite for tactile pressure sensing Journal Article
In: Nanoscale, vol. 11, pp. 2779-2786, 2019.
@article{Li2019,
title = {Ultrasensitive, flexible, and low-cost nanoporous piezoresistive composite for tactile pressure sensing},
author = {Jing Li and Santiago Orrego and Junjie Pan and Peisheng He and Sung Hoon Kang},
url = {https://pubs.rsc.org/en/content/articlepdf/2014/NR/C8NR09959F?page=search},
doi = {10.1039/C8NR09959F.},
year = {2019},
date = {2019-01-02},
journal = {Nanoscale},
volume = {11},
pages = {2779-2786},
abstract = {Highly sensitive flexible tactile sensors are of continuing interest for various applications including wearable devices, human- machine interface, and internet of things. Current technologies for high sensitivity piezoresistive sensors rely on costly materials and/or fabrication methods such as graphene-based and micro-structured composites limiting accessibility and scalability. Here, we report a facile sacrificial casting-etching method to synthesize nanoporous carbon nanotube/polymer composites for ultra-sensitive and low-cost piezoresistive pressure sensors. Our synthesis method overcomes the limitations of traditional solution-dip-coating method for adhering nanoscale conductive materials to the nanoscale porous surface. Importantly, we show ultra-high sensitivity with a strain gauge factor over 300, which is ~50 times higher than that of traditional CNT-based piezoresistive sensors and ~10 times higher than most of graphene-based ones. For practical tactile sensing applications, we demonstrate that the sensors can detect both gentle pressures (1 Pa-1 kPa) and low-pressure (1 kPa-25 kPa) with a fraction of cost. Our nanoporous polymer composite could contribute to expanding the scope of using nanocomposites for applications including subtle locomotion sensing, interactive human-machine interface systems, and internet of things from its easy tunability for sensing diverse range tactile signals.},
keywords = {},
pubstate = {published},
tppubtype = {article}
}
Li, Jing; Zhu, Zhiren; Fang, Lichen; Guo, Shu; Erturun, Ugur; Zhu, Zeyu; West, James E; Ghosh, Somnath; Kang, Sung Hoon
Analytical, numerical, and experimental studies of viscoelastic effects on the performance of soft piezoelectric nanocomposites Journal Article
In: Nanoscale, vol. 9, pp. 14215-14228, 2017.
@article{C7NR05163H,
title = {Analytical, numerical, and experimental studies of viscoelastic effects on the performance of soft piezoelectric nanocomposites},
author = {Jing Li and Zhiren Zhu and Lichen Fang and Shu Guo and Ugur Erturun and Zeyu Zhu and James E West and Somnath Ghosh and Sung Hoon Kang},
url = {http://dx.doi.org/10.1039/C7NR05163H},
doi = {10.1039/C7NR05163H},
year = {2017},
date = {2017-09-15},
journal = {Nanoscale},
volume = {9},
pages = {14215-14228},
publisher = {The Royal Society of Chemistry},
abstract = {Piezoelectric composite (p-NC) made of a polymeric matrix and piezoelectric nanoparticles with conductive additives is an attractive material for many applications. As the matrix of p-NC is made of viscoelastic materials, both elastic and viscous characteristics of the matrix are expected to contribute to the piezoelectric response of p-NC. However, there is limited understanding of how viscoelasticity influences the piezoelectric performance of p-NC. Here we combined analytical and numerical analyses with experimental studies to investigate effects of viscoelasticity on piezoelectric performance of p-NC. The viscoelastic properties of synthesized p-NCs were controlled by changing the ratio between monomer and cross-linker of the polymer matrix. We found good agreement between our analytical models and experimental results for both quasi-static and dynamic loadings. It is found that, under quasi-static loading conditions, the piezoelectric coefficients (d33) of the specimen with the lowest Young's modulus ([similar]0.45 MPa at 5% strain) were [similar]120 pC N-1, while the one with the highest Young's modulus ([similar]1.3 MPa at 5% strain) were [similar]62 pC N-1. The results suggest that softer matrices enhance the energy harvesting performance because they can result in larger deformation for a given load. Moreover, from our theoretical analysis and experiments under dynamic loading conditions, we found the viscous modulus of a matrix is also important for piezoelectric performance. For instance, at 40 Hz and 50 Hz the storage moduli of the softest specimen were [similar]0.625 MPa and [similar]0.485 MPa, while the loss moduli were [similar]0.108 MPa and [similar]0.151 MPa, respectively. As piezocomposites with less viscous loss can transfer mechanical energy to piezoelectric particles more efficiently, the dynamic piezoelectric coefficient (d[prime or minute]33) measured at 40 Hz ([similar]53 pC N-1) was larger than that at 50 Hz ([similar]47 pC N-1) though it has a larger storage modulus. As an application of our findings, we fabricated 3D piezo-shells with different viscoelastic properties and compared the charging time. The results showed a good agreement with the predicted trend that the composition with the smallest elastic and viscous moduli showed the fastest charging rate. Our findings can open new opportunities for optimizing the performance of polymer-based multifunctional materials by harnessing viscoelasticity.},
keywords = {},
pubstate = {published},
tppubtype = {article}
}
Note: Send e-mail to Prof. Kang at [email protected] if you need a pdf file of the papers below.
2019
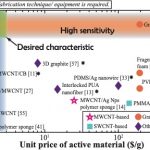
Li, Jing; Orrego, Santiago; Pan, Junjie; He, Peisheng; Kang, Sung Hoon
Ultrasensitive, flexible, and low-cost nanoporous piezoresistive composite for tactile pressure sensing Journal Article
In: Nanoscale, vol. 11, pp. 2779-2786, 2019.
Abstract | Links | BibTeX | Tags: composite, porous, pressure, Sensor, soft, stretchable electronics
@article{Li2019,
title = {Ultrasensitive, flexible, and low-cost nanoporous piezoresistive composite for tactile pressure sensing},
author = {Jing Li and Santiago Orrego and Junjie Pan and Peisheng He and Sung Hoon Kang},
url = {https://pubs.rsc.org/en/content/articlepdf/2014/NR/C8NR09959F?page=search},
doi = {10.1039/C8NR09959F.},
year = {2019},
date = {2019-01-02},
journal = {Nanoscale},
volume = {11},
pages = {2779-2786},
abstract = {Highly sensitive flexible tactile sensors are of continuing interest for various applications including wearable devices, human- machine interface, and internet of things. Current technologies for high sensitivity piezoresistive sensors rely on costly materials and/or fabrication methods such as graphene-based and micro-structured composites limiting accessibility and scalability. Here, we report a facile sacrificial casting-etching method to synthesize nanoporous carbon nanotube/polymer composites for ultra-sensitive and low-cost piezoresistive pressure sensors. Our synthesis method overcomes the limitations of traditional solution-dip-coating method for adhering nanoscale conductive materials to the nanoscale porous surface. Importantly, we show ultra-high sensitivity with a strain gauge factor over 300, which is ~50 times higher than that of traditional CNT-based piezoresistive sensors and ~10 times higher than most of graphene-based ones. For practical tactile sensing applications, we demonstrate that the sensors can detect both gentle pressures (1 Pa-1 kPa) and low-pressure (1 kPa-25 kPa) with a fraction of cost. Our nanoporous polymer composite could contribute to expanding the scope of using nanocomposites for applications including subtle locomotion sensing, interactive human-machine interface systems, and internet of things from its easy tunability for sensing diverse range tactile signals.},
keywords = {composite, porous, pressure, Sensor, soft, stretchable electronics},
pubstate = {published},
tppubtype = {article}
}
2017
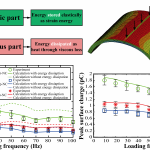
Li, Jing; Zhu, Zhiren; Fang, Lichen; Guo, Shu; Erturun, Ugur; Zhu, Zeyu; West, James E; Ghosh, Somnath; Kang, Sung Hoon
Analytical, numerical, and experimental studies of viscoelastic effects on the performance of soft piezoelectric nanocomposites Journal Article
In: Nanoscale, vol. 9, pp. 14215-14228, 2017.
Abstract | Links | BibTeX | Tags: analytical, composite, energy harvesting, experimental, mechanics of soft materials and structures, numerical, piezoelectric, sensing, viscoelasticity
@article{C7NR05163H,
title = {Analytical, numerical, and experimental studies of viscoelastic effects on the performance of soft piezoelectric nanocomposites},
author = {Jing Li and Zhiren Zhu and Lichen Fang and Shu Guo and Ugur Erturun and Zeyu Zhu and James E West and Somnath Ghosh and Sung Hoon Kang},
url = {http://dx.doi.org/10.1039/C7NR05163H},
doi = {10.1039/C7NR05163H},
year = {2017},
date = {2017-09-15},
journal = {Nanoscale},
volume = {9},
pages = {14215-14228},
publisher = {The Royal Society of Chemistry},
abstract = {Piezoelectric composite (p-NC) made of a polymeric matrix and piezoelectric nanoparticles with conductive additives is an attractive material for many applications. As the matrix of p-NC is made of viscoelastic materials, both elastic and viscous characteristics of the matrix are expected to contribute to the piezoelectric response of p-NC. However, there is limited understanding of how viscoelasticity influences the piezoelectric performance of p-NC. Here we combined analytical and numerical analyses with experimental studies to investigate effects of viscoelasticity on piezoelectric performance of p-NC. The viscoelastic properties of synthesized p-NCs were controlled by changing the ratio between monomer and cross-linker of the polymer matrix. We found good agreement between our analytical models and experimental results for both quasi-static and dynamic loadings. It is found that, under quasi-static loading conditions, the piezoelectric coefficients (d33) of the specimen with the lowest Young's modulus ([similar]0.45 MPa at 5% strain) were [similar]120 pC N-1, while the one with the highest Young's modulus ([similar]1.3 MPa at 5% strain) were [similar]62 pC N-1. The results suggest that softer matrices enhance the energy harvesting performance because they can result in larger deformation for a given load. Moreover, from our theoretical analysis and experiments under dynamic loading conditions, we found the viscous modulus of a matrix is also important for piezoelectric performance. For instance, at 40 Hz and 50 Hz the storage moduli of the softest specimen were [similar]0.625 MPa and [similar]0.485 MPa, while the loss moduli were [similar]0.108 MPa and [similar]0.151 MPa, respectively. As piezocomposites with less viscous loss can transfer mechanical energy to piezoelectric particles more efficiently, the dynamic piezoelectric coefficient (d[prime or minute]33) measured at 40 Hz ([similar]53 pC N-1) was larger than that at 50 Hz ([similar]47 pC N-1) though it has a larger storage modulus. As an application of our findings, we fabricated 3D piezo-shells with different viscoelastic properties and compared the charging time. The results showed a good agreement with the predicted trend that the composition with the smallest elastic and viscous moduli showed the fastest charging rate. Our findings can open new opportunities for optimizing the performance of polymer-based multifunctional materials by harnessing viscoelasticity.},
keywords = {analytical, composite, energy harvesting, experimental, mechanics of soft materials and structures, numerical, piezoelectric, sensing, viscoelasticity},
pubstate = {published},
tppubtype = {article}
}