Publications
Li, Jing; Orrego, Santiago; Pan, Junjie; He, Peisheng; Kang, Sung Hoon
Ultrasensitive, flexible, and low-cost nanoporous piezoresistive composite for tactile pressure sensing Journal Article
In: Nanoscale, vol. 11, pp. 2779-2786, 2019.
@article{Li2019,
title = {Ultrasensitive, flexible, and low-cost nanoporous piezoresistive composite for tactile pressure sensing},
author = {Jing Li and Santiago Orrego and Junjie Pan and Peisheng He and Sung Hoon Kang},
url = {https://pubs.rsc.org/en/content/articlepdf/2014/NR/C8NR09959F?page=search},
doi = {10.1039/C8NR09959F.},
year = {2019},
date = {2019-01-02},
journal = {Nanoscale},
volume = {11},
pages = {2779-2786},
abstract = {Highly sensitive flexible tactile sensors are of continuing interest for various applications including wearable devices, human- machine interface, and internet of things. Current technologies for high sensitivity piezoresistive sensors rely on costly materials and/or fabrication methods such as graphene-based and micro-structured composites limiting accessibility and scalability. Here, we report a facile sacrificial casting-etching method to synthesize nanoporous carbon nanotube/polymer composites for ultra-sensitive and low-cost piezoresistive pressure sensors. Our synthesis method overcomes the limitations of traditional solution-dip-coating method for adhering nanoscale conductive materials to the nanoscale porous surface. Importantly, we show ultra-high sensitivity with a strain gauge factor over 300, which is ~50 times higher than that of traditional CNT-based piezoresistive sensors and ~10 times higher than most of graphene-based ones. For practical tactile sensing applications, we demonstrate that the sensors can detect both gentle pressures (1 Pa-1 kPa) and low-pressure (1 kPa-25 kPa) with a fraction of cost. Our nanoporous polymer composite could contribute to expanding the scope of using nanocomposites for applications including subtle locomotion sensing, interactive human-machine interface systems, and internet of things from its easy tunability for sensing diverse range tactile signals.},
keywords = {},
pubstate = {published},
tppubtype = {article}
}
Fang, Lichen; Li, Jing; Zhu, Zeyu; Orrego, Santiago; Kang, Sung Hoon
Piezoelectric polymer thin films with architected cuts Journal Article
In: Journal of Materials Research, vol. 33, no. 3, pp. 330-342, 2018, (Invited article on Focus Issue on Architected Materials).
@article{Fang2018,
title = {Piezoelectric polymer thin films with architected cuts},
author = {Lichen Fang and Jing Li and Zeyu Zhu and Santiago Orrego and Sung Hoon Kang},
editor = {Lorenzo Valdevit, Katia Bertoldi, James Guest, Christopher Spadaccini},
url = {https://www.cambridge.org/core/journals/journal-of-materials-research/article/piezoelectric-polymer-thin-films-with-architected-cuts/41109CD493CBADDE85D9446FCE3A95A7},
doi = {10.1557/jmr.2018.6},
year = {2018},
date = {2018-02-14},
journal = {Journal of Materials Research},
volume = {33},
number = {3},
pages = {330-342},
abstract = {Introducing architected cuts is an attractive and simple approach to tune mechanical behaviors of planar materials like thin films for desirable or enhanced mechanical performance. However, little has been studied on the effects of architected cuts on functional materials like piezoelectric materials. We investigated how architected cut patterns affect mechanical and piezoelectric properties of polyvinylidene fluoride thin films by numerical, experimental, and analytical studies. Our results show that thin films with architected cuts can provide desired mechanical features like enhanced compliance, stretchability, and controllable Poisson’s ratio and resonance frequency, while maintaining piezoelectric performance under static loadings. Moreover, we could observe maximum ∼30% improvement in piezoelectric conversion efficiency under dynamic loadings and harvest energy from low frequency (<100 Hz) mechanical signals or low velocity (<5 m/s) winds, which are commonly existing in ambient environment. Using architected cuts doesn't require changing the material or overall dimensions, making it attractive for applications in self-powered devices with design constraints.},
note = {Invited article on Focus Issue on Architected Materials},
keywords = {},
pubstate = {published},
tppubtype = {article}
}
Note: Send e-mail to Prof. Kang at [email protected] if you need a pdf file of the papers below.
2019
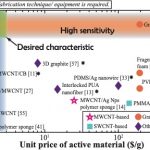
Li, Jing; Orrego, Santiago; Pan, Junjie; He, Peisheng; Kang, Sung Hoon
Ultrasensitive, flexible, and low-cost nanoporous piezoresistive composite for tactile pressure sensing Journal Article
In: Nanoscale, vol. 11, pp. 2779-2786, 2019.
Abstract | Links | BibTeX | Tags: composite, porous, pressure, Sensor, soft, stretchable electronics
@article{Li2019,
title = {Ultrasensitive, flexible, and low-cost nanoporous piezoresistive composite for tactile pressure sensing},
author = {Jing Li and Santiago Orrego and Junjie Pan and Peisheng He and Sung Hoon Kang},
url = {https://pubs.rsc.org/en/content/articlepdf/2014/NR/C8NR09959F?page=search},
doi = {10.1039/C8NR09959F.},
year = {2019},
date = {2019-01-02},
journal = {Nanoscale},
volume = {11},
pages = {2779-2786},
abstract = {Highly sensitive flexible tactile sensors are of continuing interest for various applications including wearable devices, human- machine interface, and internet of things. Current technologies for high sensitivity piezoresistive sensors rely on costly materials and/or fabrication methods such as graphene-based and micro-structured composites limiting accessibility and scalability. Here, we report a facile sacrificial casting-etching method to synthesize nanoporous carbon nanotube/polymer composites for ultra-sensitive and low-cost piezoresistive pressure sensors. Our synthesis method overcomes the limitations of traditional solution-dip-coating method for adhering nanoscale conductive materials to the nanoscale porous surface. Importantly, we show ultra-high sensitivity with a strain gauge factor over 300, which is ~50 times higher than that of traditional CNT-based piezoresistive sensors and ~10 times higher than most of graphene-based ones. For practical tactile sensing applications, we demonstrate that the sensors can detect both gentle pressures (1 Pa-1 kPa) and low-pressure (1 kPa-25 kPa) with a fraction of cost. Our nanoporous polymer composite could contribute to expanding the scope of using nanocomposites for applications including subtle locomotion sensing, interactive human-machine interface systems, and internet of things from its easy tunability for sensing diverse range tactile signals.},
keywords = {composite, porous, pressure, Sensor, soft, stretchable electronics},
pubstate = {published},
tppubtype = {article}
}
2018
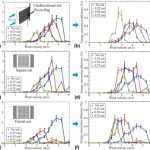
Fang, Lichen; Li, Jing; Zhu, Zeyu; Orrego, Santiago; Kang, Sung Hoon
Piezoelectric polymer thin films with architected cuts Journal Article
In: Journal of Materials Research, vol. 33, no. 3, pp. 330-342, 2018, (Invited article on Focus Issue on Architected Materials).
Abstract | Links | BibTeX | Tags: architected materials, Auxetic, energy harvesting, kirigami, mechanical metamaterial, piezoelectric, stretchable electronics, wind energy
@article{Fang2018,
title = {Piezoelectric polymer thin films with architected cuts},
author = {Lichen Fang and Jing Li and Zeyu Zhu and Santiago Orrego and Sung Hoon Kang},
editor = {Lorenzo Valdevit, Katia Bertoldi, James Guest, Christopher Spadaccini},
url = {https://www.cambridge.org/core/journals/journal-of-materials-research/article/piezoelectric-polymer-thin-films-with-architected-cuts/41109CD493CBADDE85D9446FCE3A95A7},
doi = {10.1557/jmr.2018.6},
year = {2018},
date = {2018-02-14},
journal = {Journal of Materials Research},
volume = {33},
number = {3},
pages = {330-342},
abstract = {Introducing architected cuts is an attractive and simple approach to tune mechanical behaviors of planar materials like thin films for desirable or enhanced mechanical performance. However, little has been studied on the effects of architected cuts on functional materials like piezoelectric materials. We investigated how architected cut patterns affect mechanical and piezoelectric properties of polyvinylidene fluoride thin films by numerical, experimental, and analytical studies. Our results show that thin films with architected cuts can provide desired mechanical features like enhanced compliance, stretchability, and controllable Poisson’s ratio and resonance frequency, while maintaining piezoelectric performance under static loadings. Moreover, we could observe maximum ∼30% improvement in piezoelectric conversion efficiency under dynamic loadings and harvest energy from low frequency (<100 Hz) mechanical signals or low velocity (<5 m/s) winds, which are commonly existing in ambient environment. Using architected cuts doesn't require changing the material or overall dimensions, making it attractive for applications in self-powered devices with design constraints.},
note = {Invited article on Focus Issue on Architected Materials},
keywords = {architected materials, Auxetic, energy harvesting, kirigami, mechanical metamaterial, piezoelectric, stretchable electronics, wind energy},
pubstate = {published},
tppubtype = {article}
}